You are flattening the structure of your soils and driving compaction beyond the point of recovery. Here's how you can stop it.

.jpg)
A brief absence of our hired hand this past fall gave me the opportunity to run our John Deere 2700 disk ripper on our farm. Hitched to this 9-shank ripper was an STX500 Quadtrac. During my short time as operator, I found that the ripper pulled incredibly hard, requiring me to shift into lower gears at times in order to keep moving through the heavy black soil.
“This is ridiculous,” I thought to myself. “Five-hundred horsepower turning four tracks is hardly enough to loosen this soil.”
Then, I began to think about all of the equipment that had left its tracks in this field since the season first began.
When I got home, I sat down at my computer and began mapping the tracks from every piece of equipment that had driven across the field that season.
I soon realized that over half of the ground had been squashed by a substantially heavy piece of equipment. Some places had been driven on over 5 times! I dug a little deeper and compared the axle weights, tire sizes, and tire inflation pressures of each machine. I grimaced as the reality of the situation began to take shape.
We were flattening the structure of our soils and driving compaction beyond the point of recovery.
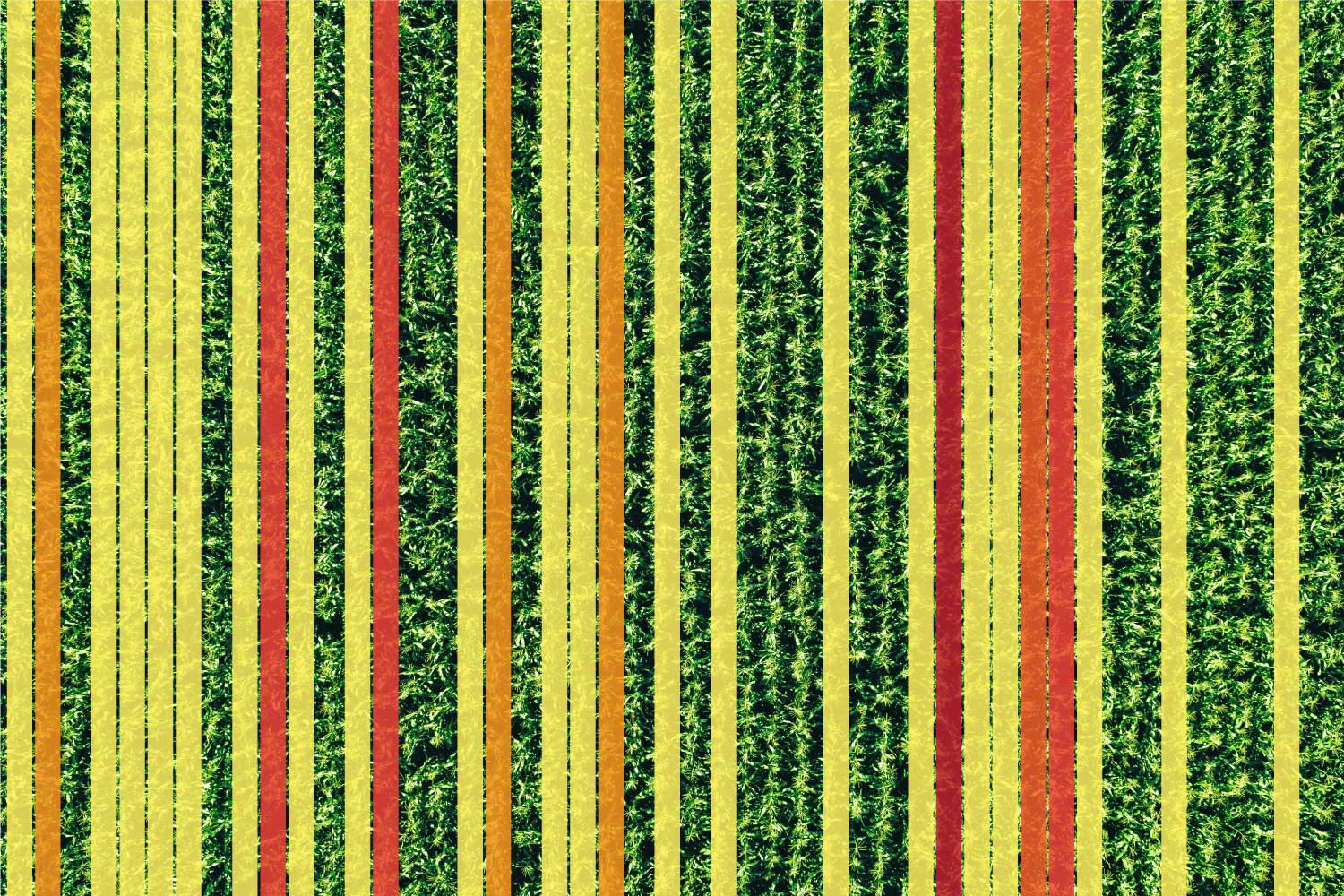
At what point does compaction become a problem?
Stop for a moment and write down the tire pressures for each major piece of equipment that drives across your field. You may not know the exact numbers, but use your best estimation.
Here is a list of equipment to help guide you:
- Fertilizer applicator
- Spring tillage tractor
- Planting tractor
- Planter carrying wheels
- Sprayer
- Combine
- Grain cart tractor
- Grain cart
- Fall tillage tractor
Scan the list and circle each item that has tire pressures above 15 PSI.
Now for each piece of equipment, write down the loaded weight and divide by the number of wheels.
Go through the list once more and circle each piece of equipment that has wheel loads greater than 10,000 lbs per wheel. (You may end up circling some equipment more than once.)
Each piece of equipment you have circled is negatively affecting your yields. Here is why.
Tire pressure drives surface soil compaction.
Tire pressures above 15 PSI compact the surface soil (0–6 inches deep) to a point where yield loss occurs. You are losing about 5 percent of your yield each year and up to 20 percent of your yield with repeated minor topsoil compaction. As a farmer, you probably won’t see or realize that this loss is taking place in your fields.
Wheel load drives subsoil compaction.
Wheel loads above 10,000 lbs per wheel drive compaction deep into the subsoil (20+ inches). This subsoil compaction causes you to permanently lose 3 percent of your yield each year—a loss you cannot recover because it is beyond the reach of tillage. And despite common thought, freeze/thaw cycles will not remove it either.
Solutions to cut compaction.
If you’re staring at a list with current tire pressures of 40, 60, or even 80 PSI (as many farmers are between planter carrying wheels and sprayer tires), don’t sweat. The technologies and strategies exist to get your tire pressures and wheel loads to where they should be (or very close to it).
“I need tracks on everything!”
It's a common thought that tracks are the boss when it comes to reducing soil compaction. They create a massive footprint that tire’s can’t come close to matching, so it’s common sense that they would compact less than tires, right?
Not necessarily. Unlike tires which are essentially floating air chambers that equally distribute the load across their entire contact area, tracks contain high pressure points under each mid-roller that drive compaction. Because of this, a machine with properly inflated tires may actually compact the soil less than one with tracks.
Now we are not against tracks. However, when you compare the cost of a machine with tracks (or the cost of retrofitting tracks onto a machine), the cost of tracks is substantially more than tires. Tracks are also more expensive and time-consuming to maintain, and add additional weight to the machine thereby making the compaction situation worse. We generally recommend tire upgrades over switching to tracks since it is a lot more feasible for most farmers and they will see similar performance.
You may also like: Tires vs. Tracks: Which Creates Less Compaction?
Central Tire Inflation Systems
We reduced the tire air pressure from 90 PSI down to 35 PSI on our John Deere DB60 planter. How? It comes down to understanding how speed impacts a tire’s required inflation pressure.
As travel speed increases, the inflation pressure required to carry the load increases. For our planter to travel at road speed, the tires require an inflation pressure of 90 PSI. At field travel speeds under 6 mph, they only require 35 PSI.
Now if you’re thinking, “there is no way I’m going to take the time to inflate and deflate all of my tires every time I enter and leave a field”, there is a convenient solution. Central tire inflation systems enable the operator to adjust the planter and tractor tires’ inflation pressures in minutes with the push of a button. Set a higher pressure for road travel, then lower the pressure for field work.
IF/VF and CFO Tires
Another way to reduce tire inflation pressure is with increased flex (IF) or very increased flex (VF) tires. IF tires can carry the same load at 20% lower air pressure than a standard radial tire, and VF tires can carry the same load at 40% lower air pressure. And if the tire has a CFO designation, you can run an even lower inflation pressure in the field.
CFO, or cyclic field operation, refers to farming operations where equipment undergoes substantial and regular axle load changes during operation. Equipment that falls under this category includes combines, grain carts, and air seeders.
By swapping our radial combine tires for IF/CFO tires, we reduced the combine tires’ inflation pressures from 40 PSI to 22 PSI with the same size tire.
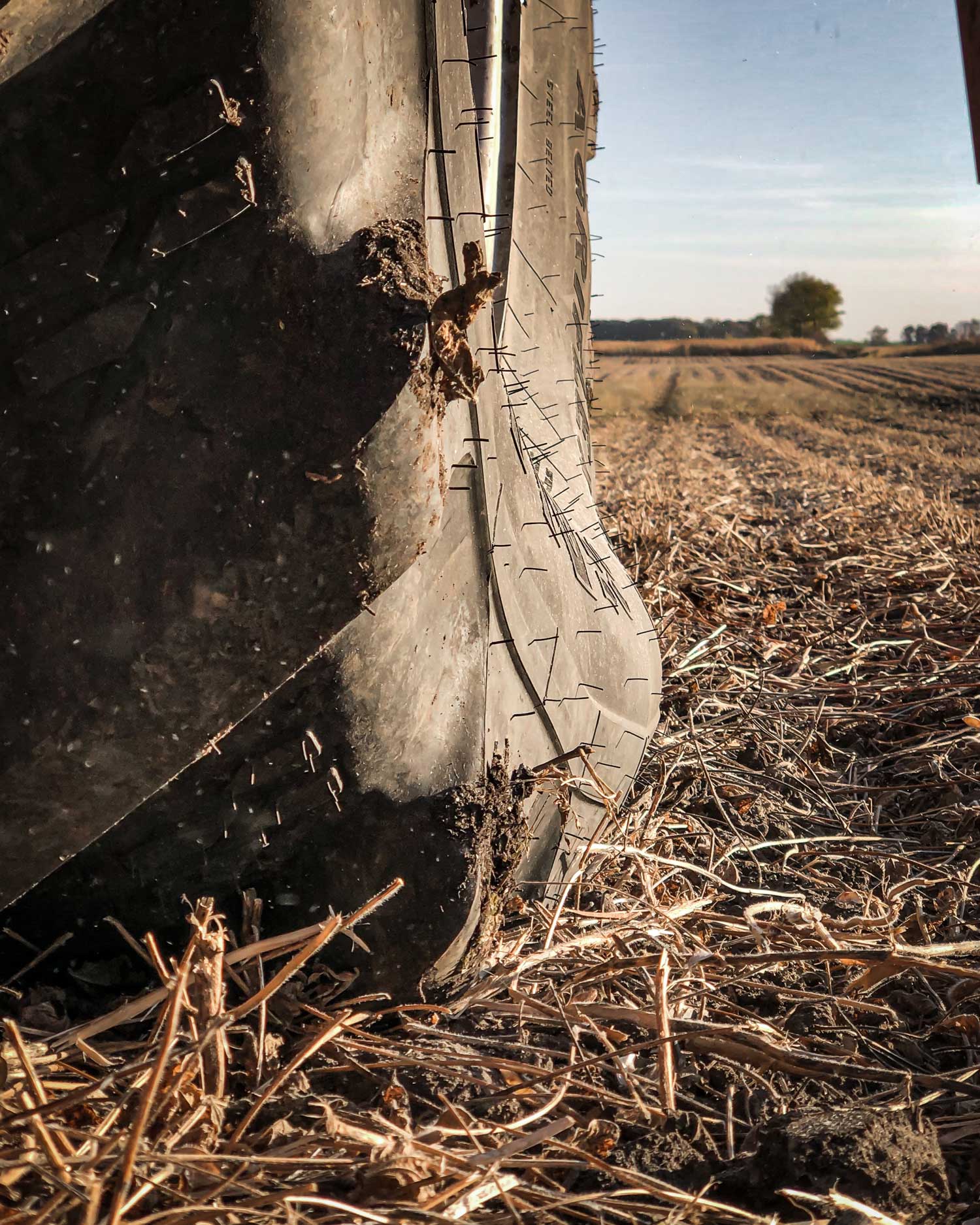
Find the best solution for your farm.
Making a smart tire investment can reduce soil compaction, cut fuel costs, and increase your yields. In some cases, these benefits pay for the cost of new tires in just one year!
If you’re not sure where you should start, reach out to our team of tire experts at NTS Tire Supply. We provide growers with solutions from every major brand of tires. We also stock the largest inventory of used and takeoff farm tires and wheels in the Upper Midwest, which means you may be able to save on your next tire or wheel purchase!
Now is an excellent time to start planning for the season ahead. Call us at (888) 787-3559 or drop us a line on our contact page. We will help you find the best solution for your operation.